製造現場改善を促す目的思考
生産性向上や品質不良対策として生産現場の改善を行う際、あるいは新たな制度を導入する際、忘れてはならないのはその「目的」です。
目的を意識しながら日々の活動を行うことで、施策・制度の本質を捉え狙った効果を発揮することが出来ます。ここでは製造の責任者や品質管理担当者を想定し、製造現場における目的思考について説明します。
1.製造部員からの質問
あなたの会社で、製造機械の点検を定期的に行うことが決まっているとします。
点検項目は点検基準によって定められ、どの程度異常が見られた場合、どのような処置を取るべきか定められています。点検は、機械を扱う作業者によって毎週及び毎月実施されています。
ある時、作業者の一人からこんな質問をされました。
「この機械を用いる製品は最近受注が無く、月に1回程度しか動かしていない。毎週点検をする必要があるのか?」
この質問に対し、どう答えるべきでしょうか?
上記の例は、以前実際に弊社コンサルタントに質問をされたものです。
ISO9001(品質マネジメントシステム)の構築・認証支援を行った企業で、若手のリーダーに対してISO9001について教えている中でのことでした。若手リーダーの一人が、自分たちが行っていることの「目的」を考え、質問をしてくれました。
ISO9001を構築している企業だと、機械点検はルールとして導入されます。ですが現場の全員が機械点検の目的を理解して導入されているとは言い難いです。これは多くの制度で同じことが言えます。
2.製造部の目的
では、機械点検は何のために行うのでしょうか?
答えは人や会社によって多少異なるかもしれませんが、一般的に「機械異常(故障)を減らす」と考えられます。
では再度考えて、何のために機械異常を減らすのでしょうか?
機械異常を減らす目的は、ざっと以下のようなことが思い浮かびます。
・機械停止時間を減らす
・機械が原因の品質不良を減らす
・作業者の安全性を高める
・長く使用する(機械の寿命を延ばす)
ここから再度考え、何のために上記のことを…と考え続けると、製造部の目的に行き当たります。
製造部は「基準に合った製品を、最少のコストで生産し続ける」ことが目的です[1]。
機械の異常を減らすことで、品質不良が減り「基準に合った製品」が生産されやすくなります。
同じように機械の異常を減らすことで、機械停止時間が減り作業者の安全性を高まることで「最少のコスト」に近づきます。
逆に言えば機械の異常が減ったとしても、メンテナンスにかかるコストがそこから得られる利益を超えるようであれば、製造部の目的に合いません。他のメンテナンス方法を考える必要があります。
つまり機械点検は「機械異常を減らす」ことを目的としながら、「基準に合った製品を、最少のコストで生産し続ける」という、より上位の目的があって行っています。
3.目的を意識した仕事
上記の目的の流れを図にすると以下のようになります。
途中の「品質不良を減らす」は企業の状況によって異なりますが、機械点検はこれらの目的に適合するように行うことで、目的に対して効果を発揮します。
では、最初の例に戻って考えてみます。
「月に1度しか使用しない機械を毎週点検する必要があるのか?」
という質問でした。
点検の目的は「機械の異常を減らす」から「基準に合った製品を、最少のコストで生産し続ける」まであります。これらに適合する形で点検を見直すことで、必要な点検を行いつつムダなコストを省くことが出来ます。
質問への回答は『点検の目的を考えて、ムダになっている部分は削る』という答えが妥当かと思います。具体的には「使用していなければ部品の摩耗は無いため、摩耗を見る部分は使用後のみとする」「ネジの緩みが毎週でも隔週でもほとんど変わらないのであれば隔週にする」などの変更が考えられます。
4.改めて「目的思考」とは
ここまで機械点検の具体例で目的について書いてきました。ここで一度改めて「目的を考える」ことについて説明をします。
全ての仕事には目的があります。材料調達、運搬、機械準備、加工、検査、出荷、これら(これら以外も)全てに目的があり、その目的を達成するために行っています。
そして目的にはさらに上の目的があります。機械点検の例では「機械の異常を減らす」の上に「品質不良を減らす」、さらにその上には「基準に合った製品を最小コストで生産する」という目的がありました。この「目的の目的」をここでは「上位目的」と呼びます。図にすると右のようになります。
行動・物というのは現場で行う仕事や設備・工具などです。現場にある工具は「作業をしやすくする」ことが目的でしょう。そこにはさらに目的があり「作業精度を高める」「作業時間を短縮する」などが当てはまります。
現状を改善するためには、行っている仕事や物が「目的に合っているか」「上位目的から見て適しているか」を考えることです。
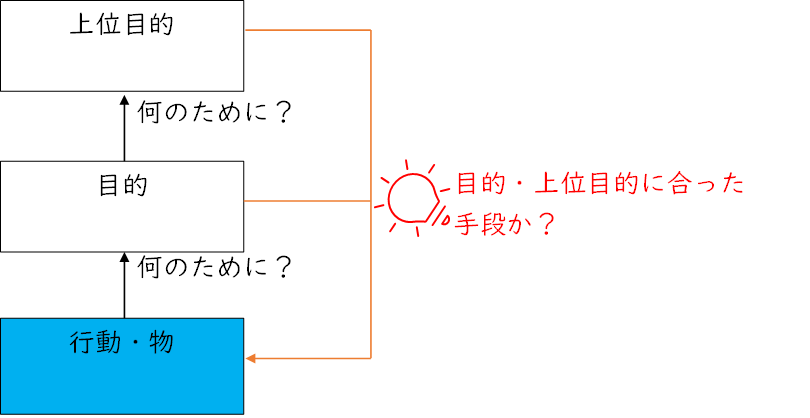
工具で言えば、破損している工具を使い続けることは工具を使わないよりは作業をしやすくし作業時間を短縮しますが、破損していない工具と比べれば適しているとは言えないかもしれません。
5.製造現場で見る目的の欠如
ここまでのことは一見当たり前に見えます。ですが実際に製造現場において目的を見失ってしまっている例を見ます。
・形式的に行っているだけのダブルチェック
・2年以上開かれていない作業手順書
・すべて〇が付けられている機械点検表
・達成のための行動がとられていない目標
あなたの会社ではこのようなことが無いでしょうか?
目的が理解されていないこれらの行動は、効果に対して手間や負担が大きくなっています。大抵これらはある時「意味が無いからやめる」という話が持ち上がり、廃止されます。
ですが本来は目的があったもので、存在が悪いのではなく目的に沿って行われていないことが悪いのです。目的を改めて認識し、目的に合うように行うことで狙っていた効果を発揮します。
6.目的思考を用いた改善の例
最後に目的を用いて改善した二つの例を紹介します。
どちらも弊社で過去に遭遇した例で、一つは製造部での不良削減、もう一つは製造現場ではありませんが調達部で行った部品コストダウンです。
例1:製造部での不良削減
ある製造ラインで生産する製品に顧客クレームがあり、調査及び改善を行うことになりました。
その日の会議では「対策実施には時間がかかるためまずは流出を止める」という流れになり、流出原因についての話になりました。というのもこのラインでは過去に同様のクレームがあり、当該部分は途中でチェックすることになっていたからです。
会議の中でチェックについて具体的に聞いていくと
『機械を止めて生産を遅らせたくないため、違和感くらいで機械は止めないし報告もしていない』
という状況が分かりました。
その後ラインのメンバーと「チェックをする目的」について話し合いました。その上で実際に機械の一時停止から立ち上がりまでにかかる時間等を調べ、不具合時に機械を止める場合と顧客クレームが発生した場合の遅れや損失の差について話をしました。
その結果「チェック担当は違和感があった際には機械を止めて確認する」という形に変え、このラインでの顧客クレーム数を低減することが出来ました。
例2:調達部でのコストダウン
ある企業の調達部で、仕入れ部品のコストダウンを進めていました。調達部によるコストダウンは通常仕入れ先交渉になりますが、この会社では発注の工夫など自社内で出来ること、仕入れ先の工程改善を仕入れ先と一緒に考えて実施することの二つを進めて改善を行っていました(得られる利益は仕入れ先と折半)。
ある調達部員は発注している部品の設計に目を付け「何のためにこの形状なのか?何のためにこの加工精度が必要なのか?」を設計担当者や組立担当者に確認しながら一つ一つ洗い出していきました。それを仕入れ先で行っている加工と照らし合わせると、製品の機能及びデザインから見て
・削らなくても良い部分を削っている
・必要以上の精度になっている
箇所を見つけることが出来ました。それを設計担当者に確認し設計変更をしてもらうことで、仕入れ先の作業時間削減及び自社のコストダウンにつなげました。
7.終わりに:製造現場のための目的思考
ここまで目的を考え、目的を意識して仕事を行うことの重要性を説明してきました。
現在行っている制度や仕事について目的を考え、目的に合うように変えていければ良いですが、現実にきっかけも無くやり方を変えることは難しいです。もし社内で小集団活動が行われているのであればその中で取り上げる、目標制度があれば半期に1項目見直す形で取り上げるなど、プロジェクトのような形で行うことをお勧めします。
また改善活動の対策立案においては【ECRSの原則】というフレームワークがあります。これは手間がかかっている作業・工程に対して、
E(Eliminate):無くせないか?
C(Conbine):類似作業と一緒にすることで効率化出来ないか?
R(Rearrange):順序を変えることで効率化出来ないか?
S(Simplify):簡素化して効率化出来ないか?
の順番で考えることで、大きな改善の効果を得られるというものです。このフレームワークを利用することで自動的に『最小のコスト』の目的に沿う案になります。
目的思考は改善における強力な武器です。
冒頭で述べたように、目的を理解して日々の活動を行うことで制度や物事の本質を捉えることが出来ます。また同時に仕事のモチベーションを高めてくれるものでもあります。
ぜひ目的を考える習慣をつけ、現場の改善に役立ててください。
[1]一般的な企業における筆者の考えを提示しています。最少のコストを目的としない(例えば最少の環境負荷など) 企業もあります。
C O N T A C T
弊社では品質管理に関する経営コンサルティングを行っています。
お問い合わせ・ご相談は以下いずれかからお願いいたします